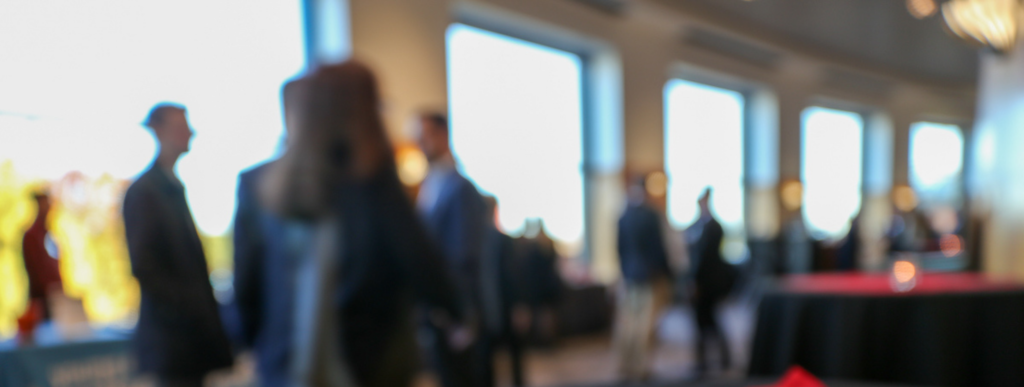
OEN Member NewsDWFritz Automation | Manufacturing Awards Excellence in Training Award winner (Portland Business Journal)
When DWFritz Automation got a huge order from an industrial partner late last year, it realized it had to ramp up its employee pool quickly.
But rapidly hiring more than 140 people is no easy task. So to meet the demand, the company came up with an unusual approach – it partnered with four of its placing agencies, training them and allowing them to place candidates without the usual DWFritz in-house team screening and interviewing.
“When we do the work we do, we sometimes have to scale up our workforce very quickly,” said Elaine Lees, vice president of talent and organizational development. “We partnered with the agencies, taught them what we were looking for, and they went out and got the employees for us.”
DWFritz tasked the agencies with finding skilled employees and contractors that could start work quickly, and asked for an eight-hour guarantee for workers who ended up unqualified or who left the job early.
“And we only had two out of 140 that we sent home,” Lees said.
It’s not unusual for DWFritz, which makes customized automation equipment and systems for a wide variety of industries, to have to hire quickly. But in this case, the ramp-up was larger than the company had ever done.
“We’re under a nondisclosure agreement,” said CEO Mike Fritz, when asked to name the customer. “But it was custom automation metrology machine installations for consumer electronics.”
Part of the rapid on-boarding plan included the creation of a pod system for training. That system broke down specific jobs, like controls technicians, into smaller subgroups with a specific focus on only one type of build. Contractors and other employees who were brought on were then partnered with senior employees who worked with them daily on the project.
“From our standpoint, the training part is making sure we have consistency across our staff members,” Fritz said.
That mix of experienced employees with newly on-boarded ones helped significantly, with only an average of 9 percent turnover throughout the hiring ramp-up, Lees said.
In 2017, the company also had a rapid ramp-up of its Chinese workforce, with an order for machine installs and upgrades in 17 locations across the country. But in China, the recruitment process is a bit different than it is in the United States, and skilled workers are harder to find.
“The people we hired had to be trained as well as they could before they got to the floor,” Lees said.
In that case, DWFritz spent a few months on remedial training for new hires. As part of that, the company set up four peer-trainers and two simulation machines where new workers could get about six weeks of basics training, followed by working onsite with the team.
That effort was so effective that this year the company has 240 fully qualified people on its Chinese team, more than it’s had in the past. And it’s ahead of schedule on maintenance, repairs, upgrades and conversions.
DWFritz also provided English language classes for workers, with about 100 participating, Lees said.
Now that both ramp-ups are over, the company once again is reducing its U.S. workforce until the next time the company has to staff up to meet a customer’s needs.
“The ones in China we’re keeping,” Lees said. “The ones here, we kept some, but it’s a ramp. So as work decreases they come off those projects and go elsewhere.”
Source: www.bizjournals.com